Flexibility with regard to variant diversity and fluctuating call-off rates
In order to meet flexibility requirements, we often use manual workpiece carrier lines for the assembly of components such as battery modules or battery management systems. This is a concept in which workers manually convey the components from station to station.The lines are usually designed in a U-shape to allow a high degree of flexibility in the use of workers. To a certain extent, this allows the number of workers to be adapted to the required production capacity. When introducing a new product, so-called ramp-up curves can easily be taken into account. Initially, only one worker is assigned to the line to operate the individual stations one after the other, and the cycle time is correspondingly high. As soon as the number of call-offs increases, also the number of workers can be gradually increased until each station is finally manned by one worker.
Thanks to the design of the line as a set-up cart system, it is also possible to simply integrate different variants on just one line. The cost-intensive components, such as screwdriver systems, are installed directly on the machine frame. The product-specific processing devices are integrated in the specially designed setup carriages.
Decisive aspects in the design of concepts with a high proportion of workers
Since the concept is designed for a high proportion of manual operations, special attention must be paid to certain points. In order to exclude the possibility of incorrect installation or even damage to components, the design must be based on coherent worker guidance. Visualizations on the operator panel or pick-by-light systems signal the next processing step to the operator. Monitoring systems that ensure the correct assembly sequence can also be used.The ESD (Electro Static Discharge) design of all components in the worker area is also crucial. Particular attention is paid to this when processing highly sensitive electrical components. The commissioning personnel at our company, but also the operators during real operation at our customer's premises, must be trained for the special requirements.
Another important point in the concept development is the ergonomic consideration of the individual stations and the realistic assessment of worker times. Here, we are supported by our in-house virtual reality system, which we use for detailed analyses during the development and design phase. In this way, ergonomics considerations are carried out virtually directly at the individual stations, gripping paths are analyzed and processing times are realistically evaluated.
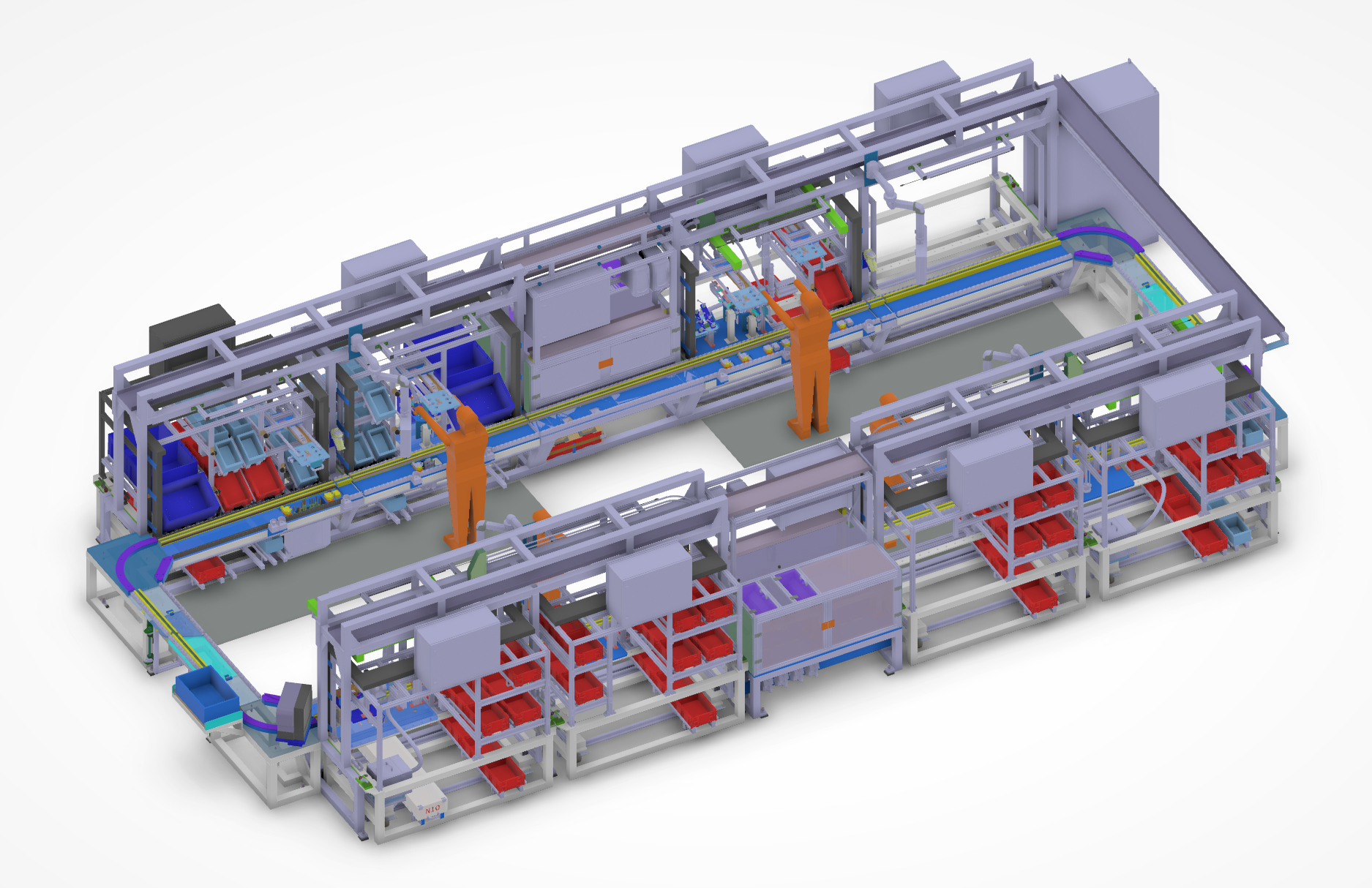