AKE's production systems offer an intelligent production concept to cover a wide variety of component variants without setup processes. Different cycle times can be implemented through scalable system concepts. Complete data acquisition and process monitoring takes place during production, which guarantees 100 percent traceability.
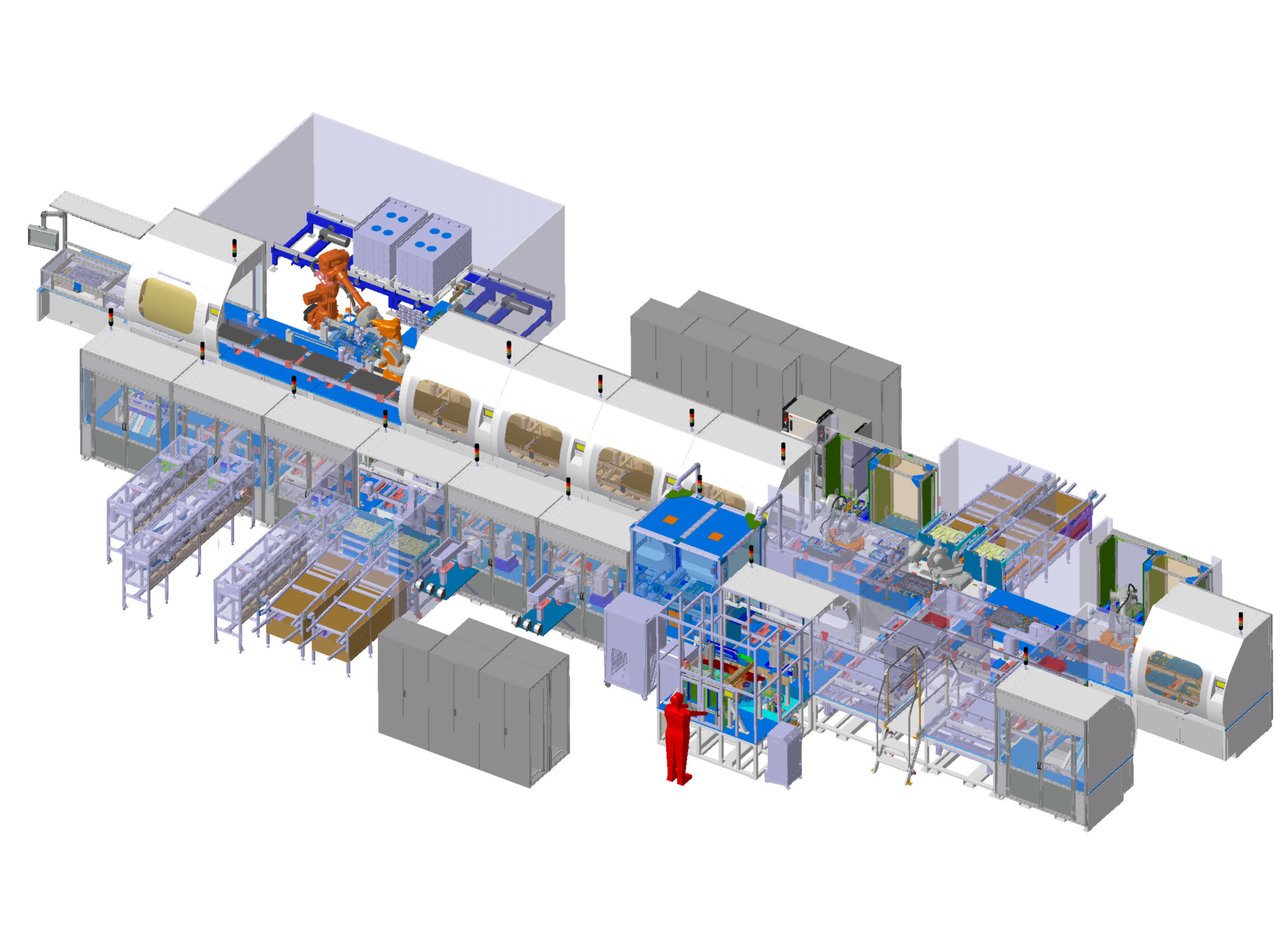
Image: Concept example of assembly system for cell connectors
In the following are examples of the processes that are integrated into our assembly systems for cell connectors:
Processes
1. Automatic feeding of various individual parts- Busbars
- Power sensors
- Temperature sensors
- Housing and carrier parts
2. Component depending pre assembly of the busbars
- Equipping taps and sensors
- Assembling
- Laser welding
- Gluing
3. Mounting of the prepared busbars in the carrier parts
4. Ultrasonic welding and hot welding
5. Depending on requirements, combination with manual assembly stations (e.g. for cable assembly) or with rework stations
6. EOL testing
- High Voltage isolation tests
- Communication testing of the sensors
7. Component marking as DMX codes and text
- Labeling
- Laser marking
8. Automatic packaging in customer containers
- Trays
- Pallets
Scope of documentation
- Batch numbers of the individual parts
- Single part tracking of safety-relevant individual parts such as HV separations
- Mounting forces and distances
- Adhesive application parameters
- Laser welding parameters
- Camera measurement results
- 2D and 3D measurement results
- Test results from electrical tests
- General information about the produced part such as individual part number, production time, product variants, and much more.