Our automation experts work out the optimum concept, taking into account the customer's requirements and the component data, and integrate the appropriate transport system for it - often a combination of different systems is also useful.
Advantages and applications of different transport systems
The double belt conveyor - the classic in automated production
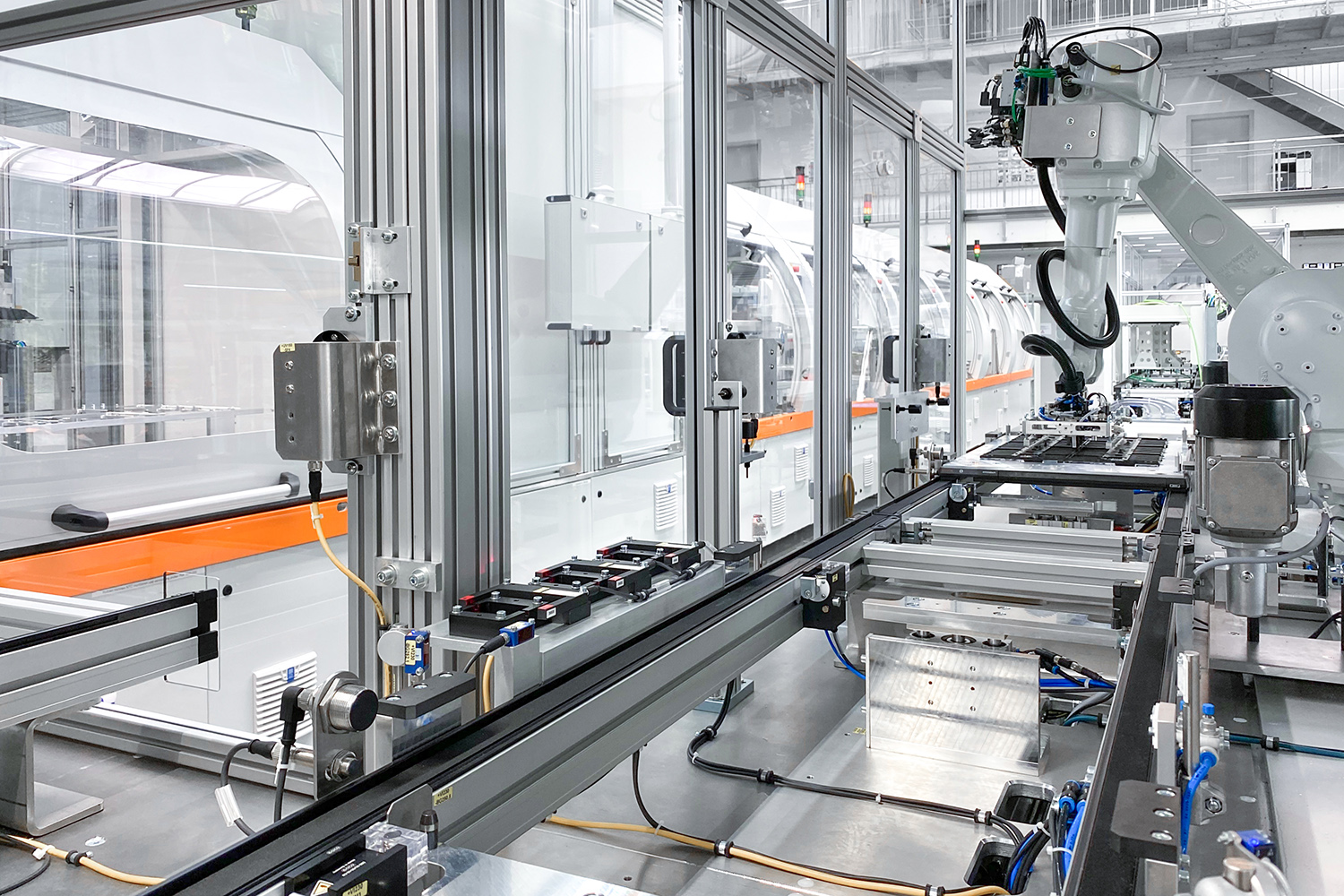
The double belt conveyor is considered to be one of the most economical solutions, especially in terms of initial costs. Installation and maintenance are also simple, as the system is a frequently used standard that is regularly installed in AKE assembly lines.
Advantages at a glance
- Low initial cost
- Easy installation and maintenance
- Modularly expandable
- Wide range of workpiece carrier sizes and loads
- Machining on the workpiece carrier also possible from below
Highest dynamics in production thanks to transport systems based on linear motors
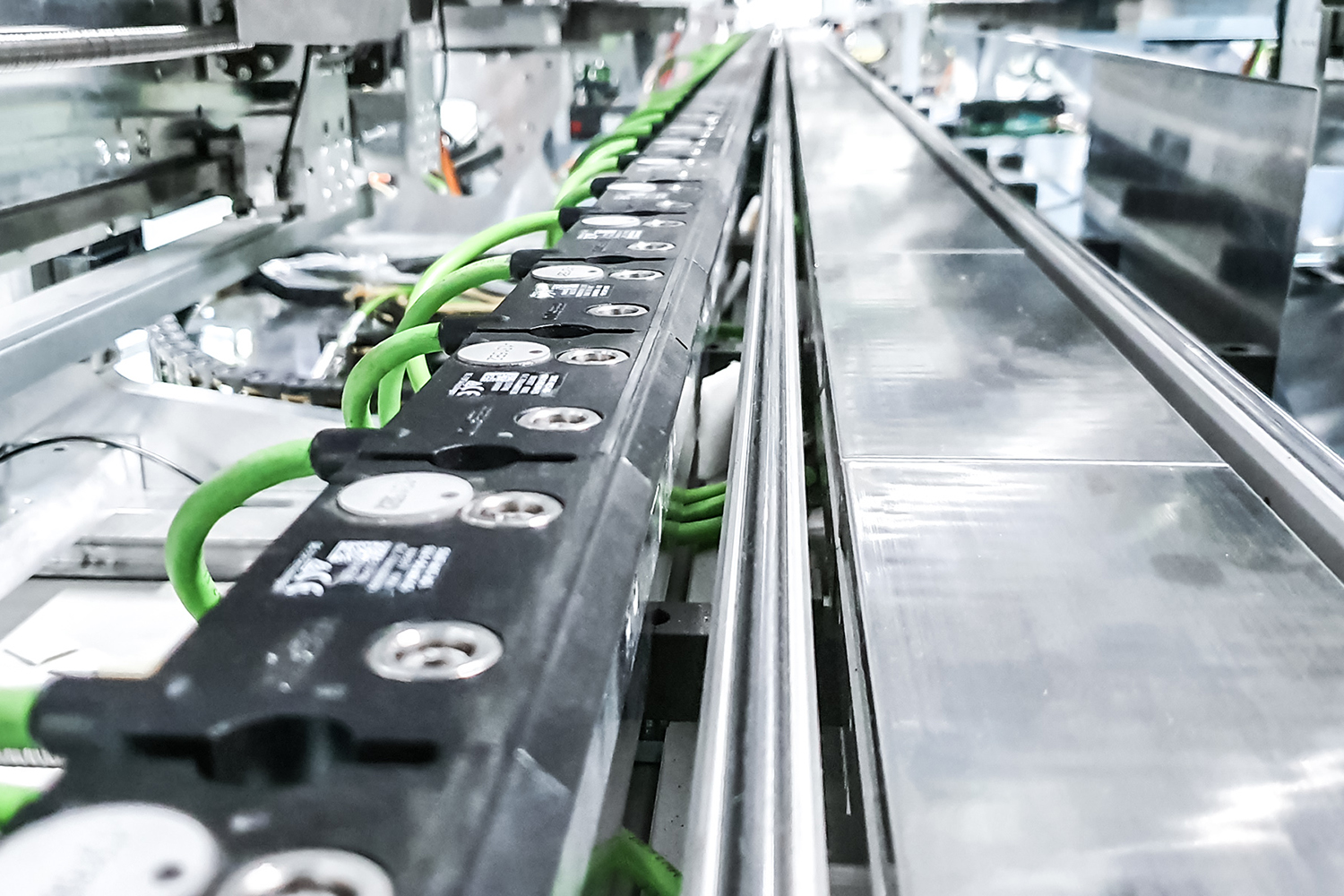
In addition, synchronization with other processes is possible, enabling on-the-fly machining. Thanks to the reduction of sill and changeover times, maximum productivity is achieved. This variant is therefore mainly used in processes that require extremely low cycle times.
Conveyor belts based on linear motors can be implemented as a hybrid solution in combination with conventional conveyor systems. By integrating them only at the process-relevant stations, the production concept is designed to be very economical overall without sacrificing any of the advantages.
Advantages at a glance
- Individual control of each carrier possible
- High speed and acceleration/deceleration
- Repeatability and high precision
- Cycle time optimized multi-stop function
- Enables "on-the-fly" processing
- Freely definable carrier movement profiles (forward and backward) and variable positioning without mechanical stoppers
- System enables shortest cycle times
Flexible and clean - monorail-based shuttle systems
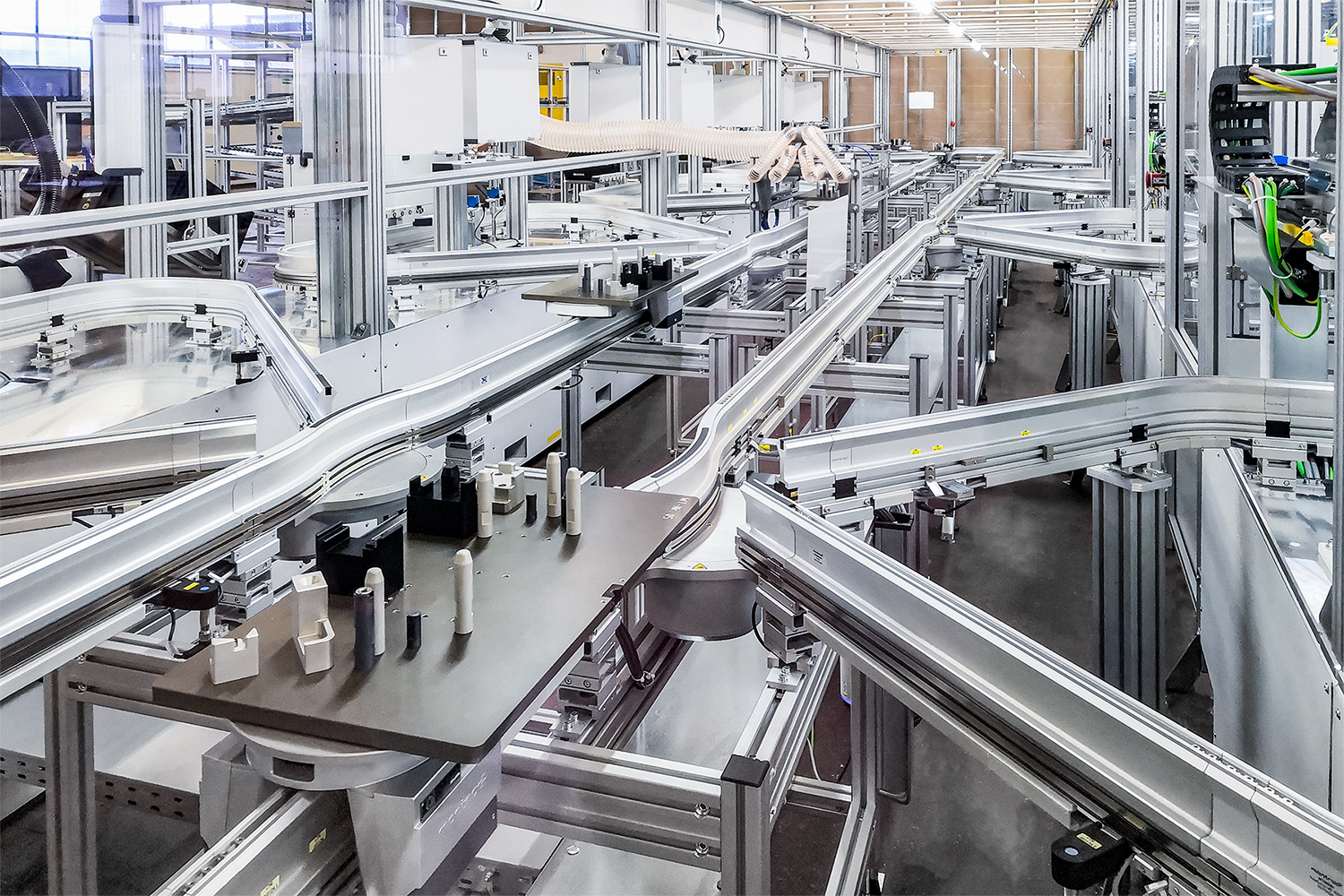
With the aid of loops and switches, stations can be approached several times and individually. The rails can be individually adapted to the space conditions and the production situation by means of curves and crossings. The shuttles offer the advantage of being able to act autonomously on the rail system thanks to their own control system and to approach the predetermined station independently. The integrated sensor technology enables anticipatory driving and prevents collisions. The system can operate on several levels through the use of inclines or lift systems, which is why it is also popular for linking systems or for component supply in intralogistics.
In addition to the flexibility and system intelligence, the low operating costs should also be emphasized. Since shuttle systems only consume energy during travel, they are very economical in operation.
Advantages at a glance
- Clean room class system
- Low energy consumption
- High flexibility and efficiency due to loops and switches
- Easy integration of buffers
- Modularly expandable
- Autonomous function of the shuttles through their own control system
- Integrated sensors for predictive driving prevent collisions
Automated guided vehicles (AGVs) in intralogistics
Automated guided vehicles are used to connect individual stations or complete assembly lines. Control is highly automatic and can be individually adapted to the situation. Simple reprogramming can be used to quickly adapt to changing conditions. The use of driverless transport systems also allows the reduction of stationary conveyor technology and offers the possibility of saving production and logistics personnel.
Integration is easy to realize. Thanks to the individual adaptation of AGVs to the existing environment, no conversion is necessary. To optimally integrate AGVs into the logistics processes of automated production, all that is required is detailed planning, reliable commissioning and regular maintenance by trained personnel.
Automated guided vehicles should not be seen as a replacement for conventional transport systems, but rather as a supplement to further optimize logistics processes in production.
Advantages at a glance
- Improvement of the material flow
- Flexibly expandable
- No conversion of the production environment necessary – AGVs adapt to the environment
- Simple change of processes
- Saving of stationary conveyor technology
- Possibility to save production and logistics personnel
Various factors influence the choice of transport system
Each system offers its own special advantages. As independent automation experts, we always keep these in mind and design the optimum concept in close consultation with our customers. In doing so, we take into account product design, weight, required cycle times and necessary flexibility with regard to component variance and call-off numbers.
Do you have questions about the automated production of your product?
> Feel free to contact us!